Complete Machining Services adds laser mold repair services for Detroit area plastics companies
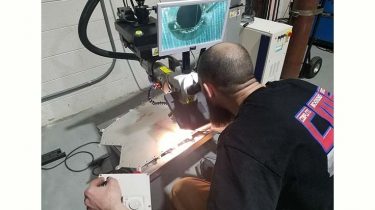
Limited Time Offer!
For Less Than the Cost of a Starbucks Coffee, Access All DevOpsSchool Videos on YouTube Unlimitedly.
Master DevOps, SRE, DevSecOps Skills!
Source:- todaysmotorvehicles.com
Davisburg, Michigan – Complete Machining Services (CMS) Inc. has added micro-laser welding services for mold repairs to serve the highest concentration of mold makers in North America in the Detroit, Michigan, to Windsor, Ontario, region.
During the past 15 years, CMS has targeted precision machining and fabricating services to market demands, typically by adding 3-, 4-, and 5-axis CNC milling machines.
CMS President and CEO Jeff Dainty says, “When your business is contract machining and fabricating, you have to have the right tools with the best level of technology to provide the needed high-quality parts manufacturing capability at a competitive cost.”
Dainty adds, “Last year we began receiving numerous requests for plastic injection mold repair services. Beyond our MIG and TIG welders, this was a capability we did not have.”
In September 2018, Dainty and CMS’ manufacturing attended IMTS 2018 in Chicago, and spent their time looking for laser welding systems for mold repair.
“After researching the laser welding systems at the show, we settled on the LaserStar 8700-3 Series Universal Jig Welding Workstation, a micro welding laser system that was going to give CMS the high-quality capability for plastic injection mold repair,” Dainty says.
LaserStar regional sales manager Gary Paresky says “We explained that they were going to need not just a laser welding machine but a workstation that provided the flexibility to handle a wide variety of parts and materials.”
Pareksy says CMS needed at least 300W to weld aluminum, requiring a fiber laser. YAG lasers are typically 200W devices.
“We directed them to our 8700-3 Series fiber laser welding workstation which provides high-peak power and optimal performance and throughput,” Paresky says. “The fiber laser source on the 8700-3 has a permanently sealed design that protects against dust and dirt, which sometimes is an issue in a job shop environment.”
He adds that the system’s laser generates little heat at the weld point, allowing laser welding smaller than 0.25mm on complex, heat sensitive intricate parts.
Dainty says, “We opted to add a number of options to the workstation that included a tower gantry for ease of moving the laser next to the molds, a motorized worktable, and a camera and monitor to aid in training operators.”